Porosity in Welding: Identifying Common Issues and Implementing Finest Practices for Prevention
Porosity in welding is a pervasive concern that often goes unnoticed till it creates substantial issues with the honesty of welds. In this discussion, we will discover the essential elements contributing to porosity development, examine its destructive impacts on weld performance, and review the best techniques that can be taken on to minimize porosity incident in welding processes.
Common Sources Of Porosity
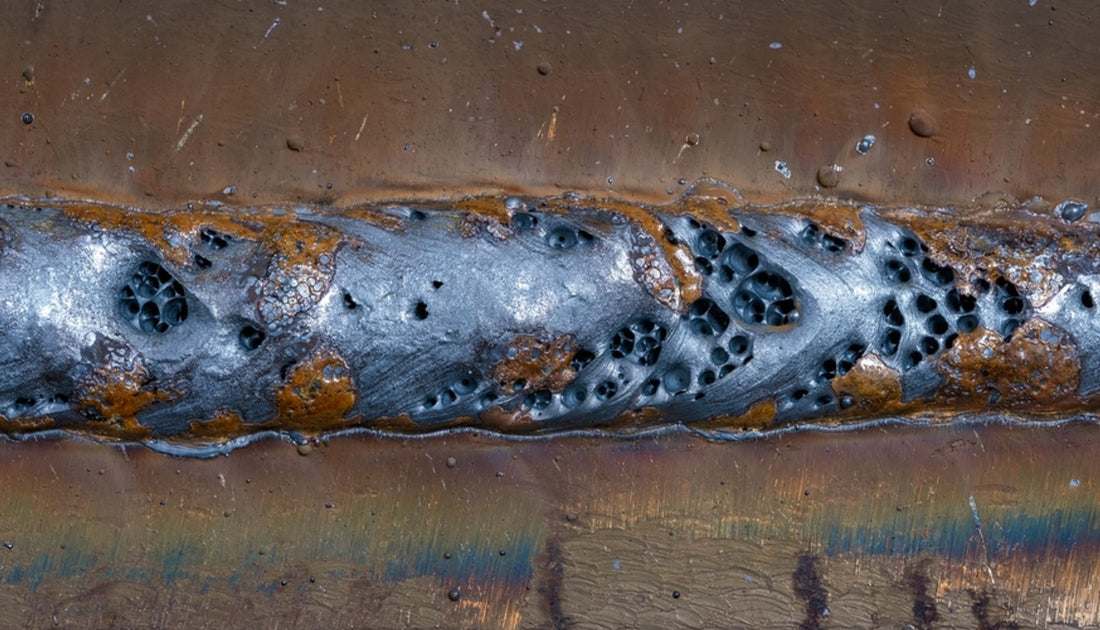
Utilizing dirty or damp filler materials can introduce pollutants into the weld, adding to porosity problems. To alleviate these typical causes of porosity, detailed cleansing of base metals, correct protecting gas selection, and adherence to optimum welding specifications are essential techniques in accomplishing top quality, porosity-free welds.
Effect of Porosity on Weld Top Quality

The existence of porosity in welding can significantly jeopardize the architectural honesty and mechanical residential or commercial properties of bonded joints. Porosity creates spaces within the weld steel, damaging its overall strength and load-bearing capability.
Welds with high porosity levels tend to exhibit reduced influence stamina and decreased ability to deform plastically prior to fracturing. Porosity can restrain the weld's capacity to successfully send pressures, leading to early weld failure and potential safety and security threats in important structures.
Best Practices for Porosity Avoidance
To boost the structural integrity and high quality of welded joints, what specific actions can be applied to lessen the occurrence of porosity throughout the welding process? Porosity prevention in welding is critical to make sure the integrity and toughness of site link the final weld. One effective technique appertains cleaning of the base steel, removing any kind of pollutants such as corrosion, oil, paint, or wetness that could cause gas entrapment. Making sure that the welding equipment remains in good condition, with tidy consumables and suitable gas circulation rates, can additionally considerably reduce porosity. Furthermore, maintaining a secure arc and regulating the welding criteria, such as voltage, present, and take a trip speed, assists develop a constant weld pool that decreases the threat of gas entrapment. Using the right welding technique for the particular product being welded, such as readjusting the welding angle and gun setting, can even more prevent porosity. Normal assessment of welds and immediate removal of any problems recognized throughout the welding process are vital techniques to avoid porosity and create high-quality welds.
Value of Correct Welding Strategies
Executing correct welding methods is paramount in making certain the architectural honesty and high quality of bonded joints, developing upon the structure of efficient porosity avoidance steps. Too much warm can lead to boosted porosity due to the entrapment of gases in the weld pool. In addition, using click now the proper welding parameters, such as voltage, present, and travel speed, is critical for attaining sound welds with minimal porosity.
Furthermore, the option of welding procedure, whether it be MIG, TIG, or stick welding, should straighten with the certain requirements of the project to guarantee optimum results. Proper cleansing and prep work of the base steel, as well as choosing the ideal filler product, are additionally vital elements of skillful welding techniques. By sticking to these best practices, welders can reduce the threat of porosity development and generate premium, structurally sound welds.

Testing and Quality Control Steps
Examining treatments are essential to spot and prevent porosity in welding, guaranteeing the strength and resilience of the final product. Non-destructive screening techniques such as ultrasonic testing, radiographic screening, and visual examination are generally employed to recognize possible flaws like porosity.
Post-weld examinations, on the other hand, examine the last weld for any flaws, consisting of porosity, and confirm that it satisfies defined standards. Implementing a detailed top quality control plan that includes detailed testing procedures and assessments is extremely important to reducing porosity problems and making sure the total quality of welded joints.
Final Thought
To conclude, porosity in welding can be an usual problem that click resources influences the top quality of welds. By identifying the common sources of porosity and carrying out finest techniques for avoidance, such as correct welding strategies and screening measures, welders can ensure top quality and reputable welds. It is important to focus on prevention techniques to lessen the event of porosity and keep the honesty of bonded frameworks.
Comments on “Comprehensive Guide: What is Porosity in Welding and Exactly How to avoid It”